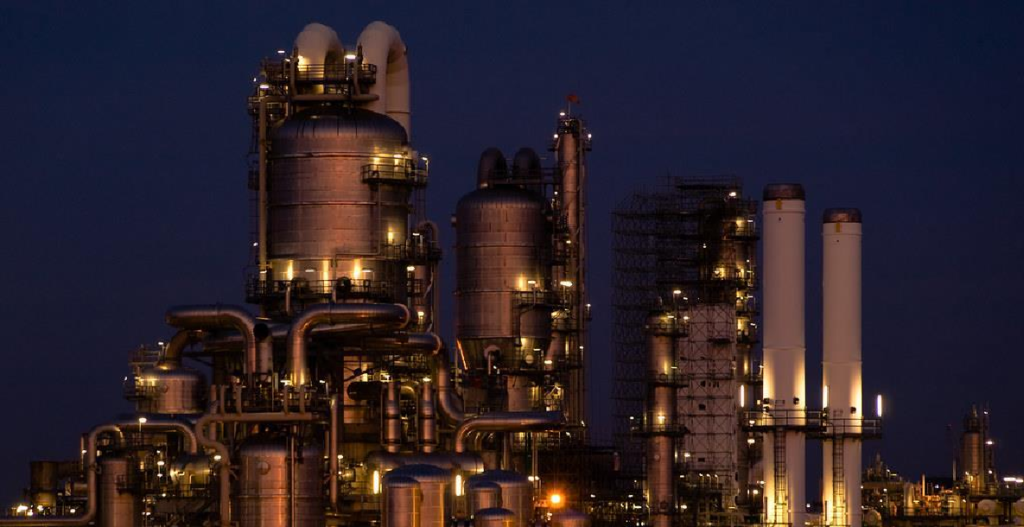
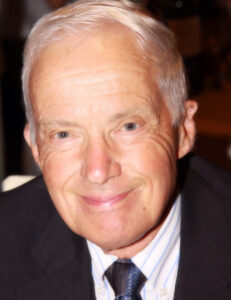
About the author
Joe Bonem is a Senior Technical Consultant at the Rosnik Solutions LLC. Joe’s 5-decade career included all phases of chemical engineering from technology to plant problem solving. His activities at the time of retirement from ExxonMobil were focused on chronic and seemingly unsolvable problems. Joe has authored 3 books – Process Engineering Problem Solving, Problem Solving for Process Operators and Specialists and Chemical Projects Scale Up: How to go from Laboratory to Commercial
Process plants often do not operate at design conditions or capacities. Deviations from utility consumptions, less than capacity operations or failure to operate at rates slightly above capacity result in higher than designed operating costs, and/or below targeted sales with subsequent loss of revenue. In addition, the less than optimum operations are often associated with an increased level of safety related incidents. A focus on “Operating Excellence” will almost always result in the following:
• Reduced operating costs due to improvements in utility, catalyst and chemical consumptions.
• Increased capacity due to focus on operating limitations. During times of sales being limited by product availability, this marginal production is the highest margin product that is produced.
• Quicker response to operating problems.
The desire to have smooth working teams and good interfaces between the various departments is important and has received significant emphasis. However, basic engineering is also important. The purpose of this series of articles is to show how engineering fits into the desire to have a well running plant. The five engineering keys to the goal of a well running plant are described as follows:
1. Steward against theoretically based metrics.
2. Monitor these metrics on a daily basis and understand all deviations from the metrics.
3. Assess the plant operations using trigger points as an alert that a problem has occurred.
4. Solve problems using a rapid response technique that is theoretically based.
5. Develop a good understanding of the equipment being used in the process.
In the interest of brevity, this article will cover the first two points only. The other keys will be covered in subsequent articles. Theoretically based metrics are those that are based on engineering calculations rather than historical operations. The theoretically based metrics can be obtained from both the original engineering design (a process design for a chemical plant) and/or a detailed engineering study of a piece of equipment (the clean heat transfer coefficient on an exchanger) These metrics are translated into the manufacturing operation using both operating procedures and operating directives. Operating Procedures are generally the specific step by step procedures that are associated with startup/shutdown and batch operations. While Operating Directives are the process set points that should be utilized in steady state normal operations. This might include areas such as feed rate or reactor temperatures.
In addition to the operating directives and operating procedures, there are also metrics that should be calculated and monitored. These might be heat transfer coefficients, compression efficiency or pump performance. All three of these equipment examples should be monitored against performance data available from the supplier. In addition to these equipment related examples, processes that involve reactors will likely require some sort of development of reaction metrics such as a reaction kinetic constant. Metrics can be developed to represent more than a single plant related variable. The example of heat transfer coefficient or reaction kinetic constant mentioned earlier are examples of this combination. More details will be provided later in a subsequent part of the five keys.
The important concept in the development of these metrics is that they must be based on engineering calculations. For example, an exothermic reactor in the chemical industry may be designed for a fixed production rate as limited by heat removal. The heat removal will likely be determined by the heat transfer coefficient. The metric for this reactor would be the design heat transfer coefficient. However, historical data may indicate that the reactor only operates at 85% of the design rate due to a heat transfer limit. Stewarding against a theoretical metric would indicate that there was a problem that should be addressed. Conversely stewarding against a historical value would indicate that there was no problem.
Since many engineering designs include some conservativeness, it is possible that the plant might be possible of running at higher rates. If this is true, then the new theoretically based metric will be this higher rate rather than the design rate. The monitoring of these metrics should be done on a daily basis either manually or using the process control computer. The value of this monitoring is twofold. It provides a means to discover and understand why the equipment is not being operated at the theoretically based metric. This might be associated with operator error or equipment malfunction (fouled heat exchanger). This discovering of deviations will provide an initial input to the 3 rd Key –“Assess the plant operations using trigger points to indicate when a problem has occurred.” A second value of this monitoring is that it provides a starting point for discussions with operating personnel concerning the validity of the metric.
The next issue will cover the daily monitoring using “trigger points” to determine if a problem is occurring.