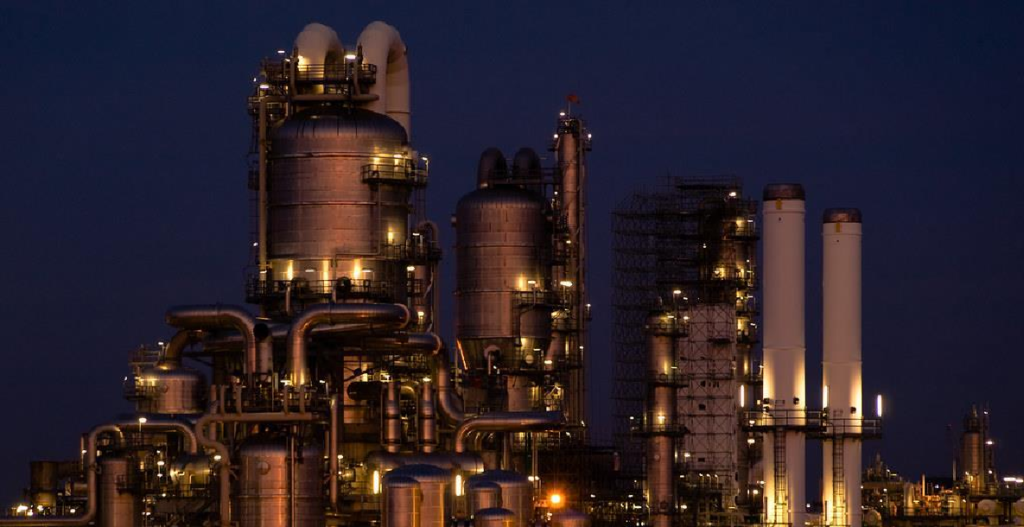
In the last of the two articles, Joe Bonem explains the importance of stewarding against theoretically based matrices and monitoring these metrics on a daily basis and understand all deviations from the metrics.
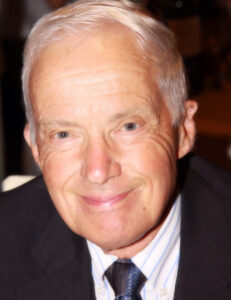
About the author
Joe Bonem is a Senior Technical Consultant at the Rosnik Solutions LLC. Joe’s 5-decade career included all phases of chemical engineering from technology to plant problem solving. His activities at the time of retirement from ExxonMobil were focused on chronic and seemingly unsolvable problems. Joe has authored 3 books – Process Engineering Problem Solving, Problem Solving for Process Operators and Specialists and Chemical Projects Scale Up: How to go from Laboratory to Commercial
In the last of the two articles, Joe Bonem explains plant monitoring using trigger points and solving the problem using a rapid response technique that is theoretically sound and based on good understanding of the equipment being used. In a previous post, I discussed the first two of the five engineering keys to get and keep your plant running well
1. Steward against theoretically based metrics.
2. Monitor these metrics on a daily basis and understand all deviations from the metrics.
3. Assess the plant operations using trigger points as an alert that a problem has occurred.
4. Solve problems using a rapid response technique that is theoretically based.
5. Develop a good understanding of the equipment being used in the process.
This post will cover development and utilization of “combined metrics”. These combined metrics in combination with “trigger points “can be used to assess plant operations. “Combined metrics” are a theoretically measure of a process variable that is obtained by calculation from both dependent and independent variables. A simple example of these “combined metrics” is the well-known heat transfer coefficient. Monitoring only the outlet temperature of a heat exchanger is not considered a theoretically based “combined metric”. Variations in this outlet temperature can be related to flow rates, incoming temperatures or the cleanliness of the heat exchanger surface. This heat transfer coefficient metric should be expressed as a percentage of the original design. If the heat transfer coefficient is followed on a daily basis, it will be possible to schedule an optimum time to clean the exchanger. A somewhat more complicated metric would be the reaction kinetics. The actual reaction kinetics can be calculated from plant data and compared to those determined in the laboratory. Again, this metric should be monitored on a daily basis and expressed as a percentage of the theoretical bench scale reaction
rate constant adjusted for continuous operation. If significant deviations from 100% occur, investigation should be initiated. This investigation might lead to focus on impurities in the feed or catalyst streams, instrumentation errors or operational
errors to name a few possibilities
This brings up the obvious question – “How big should the deviation be before an investigation is initiated?” In answering this question, the first thing to keep in mind is that this is not related to six sigma control strategy. An example of this might be an automobile concern. One rarely waits until they are 99% confident that they have a problem before they begin investigation. Determination of whether a deviation is significant enough to begin a problem-solving effort depends on both the potential seriousness of the problem and the actual deviation away from the theoretical metric. Statistical techniques can be used to determine the probability that a real problem has occurred. For example, if problem solving begins on a metric that is one sigma away from the theoretical value, there is only a 30% probability that a problem does not exist and thus a 70% probability that a problem exists. If the problem has serious consequences, it will be of value to begin problem solving even if the metric is only a single standard deviation away from the target.
While finding problems is important, it is also important to solve problems using a rapid response technique that is theoretically based. There are a multitude of problem-solving techniques. Many of them are based on one of the following:
- An analysis based purely on logic such as Ishikawa Fish Bone Diagrams.
- An analysis of chronological events using Kepner-Tregoe techniques.
- A conversation with operating or mechanical personnel with no thought of the correctness of their conclusion.
- Improper analysis of equipment data.
While there is a place for many of these techniques, any proposed problem analysis must be based on a theory. For example, I once observed an analysis of a problem associated with a fractionating column. This analysis showed that the performance problem was related to the phase of the moon. While the moon’s phases do impact tides, it is unlikely that they would affect the dynamics of a liquid contained in a vessel. When approaching a problem from a theoretical viewpoint, it is important to recognize the necessary balance between time constraints and the need to avoid “The problem went away, but it came back syndrome”. Many times, in an industrial environment, the pressures to solve the problem quickly or to “just do something” are so great that multiple things are done at once causing the problem to go away for no known reason. But since these changes
were not theoretically examined prior to implementation, the problem will reoccur at a later point in time. A much more successful approach is to do the necessary analysis and calculations to develop and support any recommendations conclusions. An example of a failure to do the necessary calculations was associated with a centrifugal compressor that appeared to be performing below design. The engineer working on this problem was familiar with the technique for the calculation of the head for a centrifugal pump. He was pressed for time by his boss telling him “We don’t want you to make a career of this. He was also confused by the various terms used to describe compression – adiabatic,
polytropic and isothermal. So, he decided to use the same equations for the centrifugal compressor as he did for pumps. This resulted in an erroneous conclusion that the wear rings should be replaced. The error was associated with the fact that the
head calculation formula for pumps (incompressible fluids) is different than the calculation formulas for compressors (compressible fluids).
This error while saving some time in the initial calculations resulted in selecting the wrong approach for solving the problem and actually caused a significant loss in time to rectify the problem. There is a difference between conclusions and hypotheses. A proposed conclusion should initially be considered a working hypothesis. Essentially all hypotheses will require verification. This verification can be done by plant tests, laboratory tests or additional calculations. Often this verification step is looked on as only successful if the proposed hypothesis is proven to be true. If the hypothesis is not verified by whatever technique is used, it is often considered a failed test. However, it should be realized that a failed test is one that does not prove or disprove the hypothesis. Conversely a test or calculation that conclusively proves or disproves the hypothesis is a successful test. Once the proposed hypothesis has been verified, it is also important to provide a means to eliminate or mitigate the problem. An example of this is an analysis that shows that a heat exchanger is fouled. This analysis should be followed with
an analysis to understand why the exchanger fouled and what should be done to eliminate/mitigate the fouling. While time pressures are always present, there are ways to develop theoretically correct hypotheses even with a time constraint. One of the ways is to use what some have referred to as a “black box approach”. This approach is especially valuable for problems associated with kinetically limited processes such as heat transfer, chemical reactions and mass transfer. This process will be described in the next issue of this series